Tupperware Before Third-Party Logistics (3PL)
Tupperware is a consumer goods line that includes food preparation, storage, and serving products for the kitchen and home. The organization lacked supply chain efficiency, had difficulty shipping products from its North Carolina plant to customers in the western United States, and needed additional warehouse space to support peak season demands.
Tupperware needed to establish effective supply chain management with third-party logistics, including integration with existing systems. They required an expert implementation partner to help achieve the following business objectives:
- Improve supply chain efficiency with quicker transportation and delivery, cost savings, and complete visibility
- Establish seamless integration between existing applications (Oracle EBS) and the third-party logistics provider (GXO)
- Increase process efficiency so that increased volume would not require additional personnel
- Set up shipping, receiving, and stock management procedures for the western United States
We have finalized our first week of GO LIVE with GXO and have now 100% of the west cost states up & running!!! OUTSTANDING work from the entire TEAM involved in this project!!! BIG CONGRATS to ALL!!!"
Juan Camilo Samacá Vice President, Supply Chain Americas, Tupperware Brands CorporationWe have finalized our first week of GO LIVE with GXO and have now 100% of the west cost states up & running!!! OUTSTANDING work from the entire TEAM involved in this project!!! BIG CONGRATS to ALL!!!"
Juan Camilo Samacá Vice President, Supply Chain Americas, Tupperware Brands CorporationSolution & Benefits of Third-Party Logistics Integration in the Consumer Goods Industry
AST’s deep experience in supply chain solutions and understanding of the consumer goods industry led the team to a successful implementation of GXO Third-Party Logistics, automating Tupperware’s inbound and outbound logistics. The team also configured and initiated operations in a new inventory organization for improved efficiency and greater customer service.
Newly built integration between GXO and Oracle EBS enables seamless data transfer between the client’s systems, and modern automation allows effective communication with customers regarding order status.
Tupperware has also achieved the following key objectives as part of its logistics modernization with AST:
- 20% of existing order lines fulfilled from new warehouse without additional effort
- Cost savings in fulfillment
- Complete visibility into logistics tracking
Solution Components:
- GXO Third-Party Logistics
- Oracle E-Business Suite
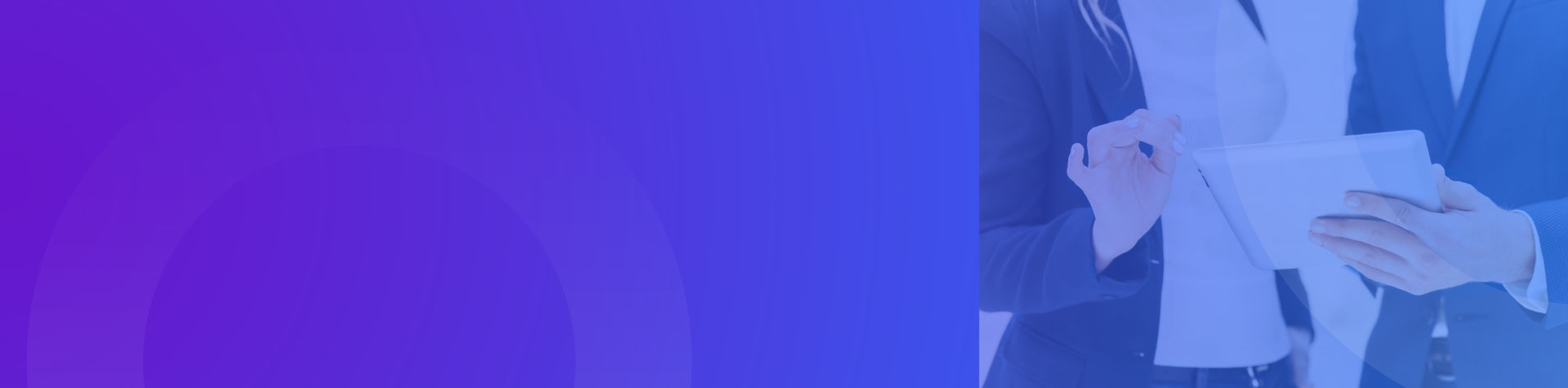
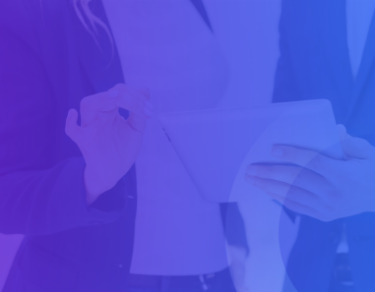
Why AST?
AST’s expertise in supply chain solutions and insight into the consumer goods industry led the team to a successful implementation of GXO Third-Party Logistics and automation of Tupperware’s logistics, including the configuration of a new inventory organization for improved efficiency and greater customer service.